特斯拉作为车企最初在电池技术积累较少,其只能通过对外采购电池,基于一致性、成本、安全性等要素,其一开始选用了松下的18650圆柱电池路线,并自主开发BMS电池管理系统。后来为不断满足消费者对更长续航里程要求,提高电池空间利用率,降低成本,双方在18650电池基础上升级至21700电池。
动力电池作为电动车核心零部件,特斯拉为了保障供应链安全性,掌握电池技术:一方面,增加外部电池供应商:从松下单一供应商,新增LG化学(2019年)和宁德时代(2020.7);另一方面,重视锂电池技术,通过引入Jeff Dahn研究团队(Jeff Dahn是目前国际上锂离子电池材料研究领域最著名的学者之一),全方位从技术、生产工艺布局锂电池领域,自建电池厂。
2019.02,通过收购干电极与超级电容企业Maxwell涉足电池生产;
2020.01,宣布自建1条电池试验线,自建电池厂;
2020.02,宣布动力电池自建项目Roadrunner。
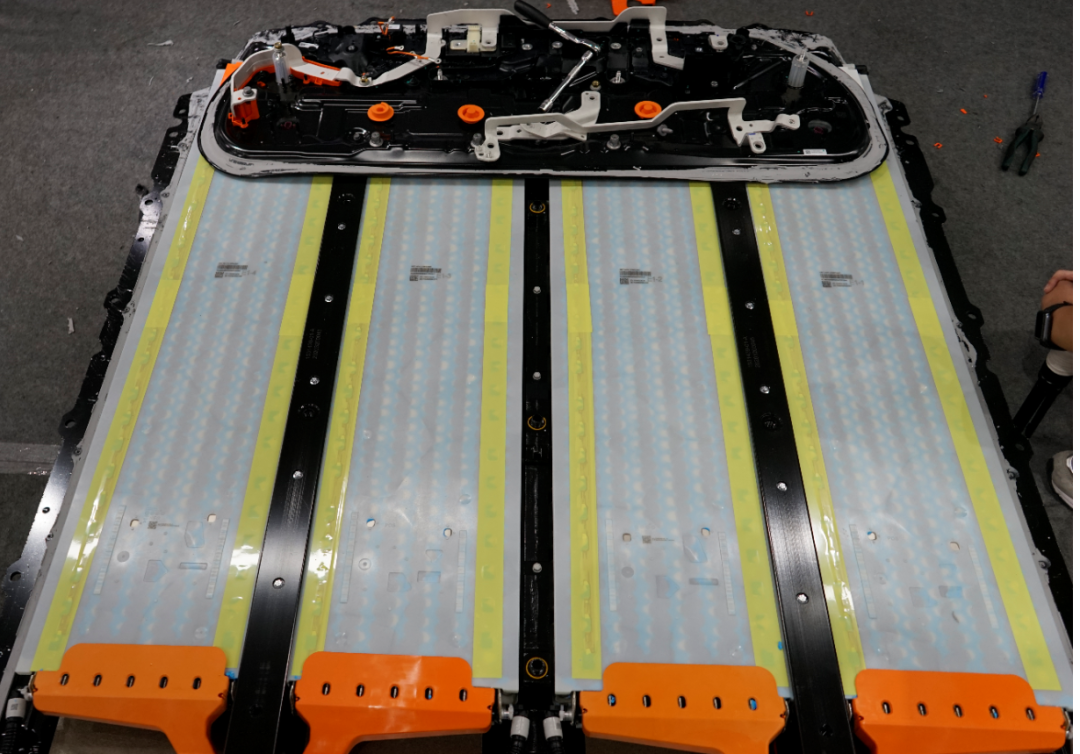
特斯拉公司的发展的矛头都指向了电极材料领域,从最近特斯拉公司的举动来看,最近所有举动都是为了摆脱高价钴的依赖,为以后生产高镍正极和硅碳负极做布局。为实现超长续航里程和长循环寿命,特斯拉做了以下方面的工作:
1.优化三元正极材料的合成方案和设计合理的原子比来提高电极材料的稳定性和降低容量衰减率。
2.优化电解液添加剂,来稳定电池充放电中的电极材料的结构,以增强电池循环寿命。目前特斯拉已经形成自有独特的电解液添加剂体系。
3.大电池组的使用和设计,以及新的成组方案也是Tesla目前最重视的领域,也能从电池组的设计上提升续航能力。
4.硅碳负极材料的应用,硅碳负极材料具有极高的理论比容量(4200mAh/g),因此对于新能源电动汽车的续航提升贡献较大。但是目前硅碳负极存在很大的不稳定性,依然很难大规模应用。
特斯拉一直都是走在硅碳电极研发和使用的前列,科研瓶颈一旦突破将给新能源动力电池带来较大的提升。
电池生产工艺——或采用干电极生产技术
含义:干电极技术就是有区别于湿法电极技术,干电极技术是摒弃了湿法电极技术中的有机溶剂(NMP),直接将少量(5%-8%)细粉状PTFE粘合剂与正极/负极粉末粘合,通过挤压机形成薄的电极材料带,再将电极材料带层压到金属箔集电体上形成成品电极。
优势:
1.降低成本,极大简化了传统湿电极制作流程,提升电池能量密度。该工艺不需要溶剂干燥箱,大幅提高生产效率,降低成本;每年或将增加20,000个100kWh的电池包产能;
2.干电极技术对高镍正极和硅碳负极的优化都是关键技术;
①利于负极补锂:可以制备更高能量密度的电极,并且有利于负极补锂。目前传统的负极补锂技术是通过静电喷涂的形式,干电极技术的使用可以将锂金属直接添加到负极材料中,改善目前的补锂技术。
②降低正极加工成本:高镍正极材料对空气中的水分异常敏感,所以传统湿法电极制备工艺对于高镍正极材料的制备通常会耗费更大的加工成本。
3.可以为后续发展固态电极提供有力支撑;
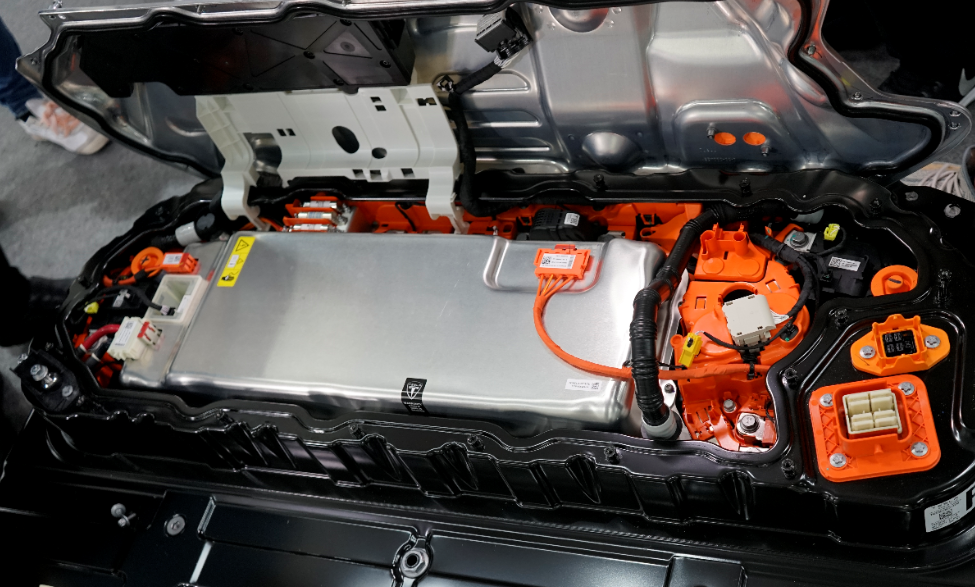
无钴电池技术
特斯拉研究团队提出可以通过制备工艺和其他代替金属的使用来弱化钴对锂电池的稳定性和性能方面的提升的效果,从而提出了对锂电池摆脱钴的愿景。而结果表明:经过优化后,在Al,Mn,Mg元素合理存在的情况下,Co的使用对抑制正极材料的相变起到的作用甚小。
特斯拉的电池从18650到21700,一直都在坚持通过“大圆柱”提升电池能量密度、降低电池成本的策略。然而,无论基于电池安全性亦或其他问题,特斯拉电池核心供应商松下与LG化学迟迟未能突破21700以上的“大圆柱”。
9月22日,特斯拉电池日上,马斯克表示特斯拉可能推出的电芯尺寸可能是现有21700的2倍;该电芯名为“饼干盒”(Biscuit Tin)大圆柱电芯。在本次活动上,特斯拉发布全新“4680”型电池,续航里程提高16%,能量密度提升5倍,电力相比有极耳提升6倍,新电池能将每千瓦时的成本降低14%。这是特斯拉自己设计的无极耳电池48毫米直径,80毫米高。新的“4680电池”将需要大约一年的时间来达到1千兆瓦的产能,但特斯拉正在考虑提高到每年2千兆瓦。
与国内学术界追求全固态电池不同,它取消了产生很多热能的极耳,解决了高能量密度的散热问题。长度为80mm,能量密度提升5倍,电力相比有极耳提升6倍,而在此之前马斯克在社交媒体上表示,电池日上所有产品均要到2022年实现量产。
我们认为,该电芯设计,与宁德时代CTP、比亚迪刀片电池一样,其核心想法均是从结构上进行创新,通过采用大电芯方式,降低成本,提高集成效率,提升体积能量密度和重量能量密度;

“无极耳”,极耳去哪了?
2020年5月特斯拉一项专利披露,将传统圆柱电芯的极耳结构取消,采用“无极耳”卷芯结构。根据特斯拉“无极耳”专利分析,极耳与集流体不成比例的导电面积,以及独立、长条形的极耳设计是当前电池的局限性。当电流必须一直沿着阴极或阳极流到极耳并流出电池单元时,电阻也会随着距离的增加而相应提高。此外,由于极耳是额外的零件,因此增加了成本并带来了制造难度。
无极耳电池能快速解决散热问题,释放能量,从而能量密度加速提升5倍以上,电力方面也是大大提升,相比有极耳提升6倍。无极耳新型电池技术不单是改变电极材料用料、也较大程度改进电池的设计生产集成工艺技术水平。
然而,详细分析特斯拉“无极耳”卷芯结构可以发现:
1.“无极耳”卷芯下端一极:集流体末端留白未涂覆正/负极材料,该处集流体部分应统统理解为广义的极耳,国内方形电池生产过程中也多采用直接切割集流体作为极耳与壳体进行连接,特斯拉“无极耳”设计的关键是极耳传导面积与集流体完全一致,甚至通过盖板多样化结构设计使极耳接触面积、传导面积大于集流体传导面积。
2.“无极耳”卷芯上端一极:若仅采用一个电极无极耳方案,上端仍与18650、21700卷芯设计一样,通过一个导电极耳与外部进行连接。按专利分析,仅一端进行无极耳连接就可以实现内阻减小5倍效果。
有业内人士表示,特斯拉“饼干盒”与近期出现的国内某超巨的细长型圆柱电池整体设计理念基本一致。特斯拉“无极耳”电池也并非真的没有极耳,而是通过巧妙的结构设计直接利用整个集流体尾部作为极耳,并通过盖板(国内称“集流盘”)结构设计增大极耳传导面积及其连接处的连接面积、缩短极耳传导距离。
因此,“无极耳”实质与国内圆柱全极耳电池的设计理念基本一致,都是通过集流体与电池壳体或集流盘的全面积、直接接触式连接,从而达到大幅降低电池内阻的效果,只是“全极耳”的连接形式更为多样化,从某种意义上说特斯拉“无极耳”可以理解为一种特定形式的“全极耳”。
全极耳,中国圆柱全极耳电池发展
国内圆柱全极耳锂离子电池最早在2003年开始萌芽,出现了正负极片单边留白、错位卷绕后形成极耳然后焊接在导电集流盘边缘的结构设计,但由于极耳形态不规则,电池生产工艺复杂,未能转化为实际产品。2009年国内开始有电池企业与装备企业共同投入圆柱全极耳研究,并真正形成了圆柱全极耳初始产品。
经过十几年的发展,国内已经形成了圆柱全极耳软连接与硬连接两种主流的连接形式,也有一端采用软连接一端采用硬连接的结合形式;其中软连接方式是汇集电流的集流盘带有一段宽而短的极耳连接壳体,硬连接方式多通过集流盘直接与壳体进行物理接触或机械连接,硬连接方式多属于“无极耳”连接。
从规格和工艺来看,圆柱全极耳电池主要包括:
1.外壳材质:钢壳,多应用于三元电池;铝壳,多应用于磷酸铁锂、锰酸锂等电池。
2.封装工艺:机械滚槽与卷边封口,多应用于10AH以下电池;激光焊接,各类电池均有应用。
3.壳体带电与结构形式:外壳带电,主要包括平底+凸帽、平底+平帽、平底+螺母等形式;外壳不带电,主要包括两端螺母、两端螺柱、两端平帽等形式。
|
|
|
|
|
|
|
|
|
|
|
与松下共投资50亿美元,建设动力电池超极工厂Gigafactory1规划35GHh
|
|
引入达尔豪斯大学Jeff Dahn团队,与其团队签订为期五年的验家合同
|
|
|
|
|
|
以2. 18亿美元滥价55%收购超级电容生产商Maxell
|
|
达尔最斯大学发布电池寿命达100万英里,并在电网储能中可种续20年
|
|
|
|
|
|
|
|
宣布在加州弗里学特建造一条试点电池生产线。发布动力电池自建项目"RoedRurner"
|
|
与CATL签订3年供货动力电池产品的协议。供货期为2020.7.1-2022.6.30
|
|
计划扩大合资电池厂gigal产能,仍处于讨论阶段:
|
|
|
|
与嘉能可Glencore达成协议,每年将采购6000吨估
|
|
松下与特斯拉计划断增Gigal工厂电池产能,预计2021年投产,产能增加10%。
|
|
|